行业新闻
提高汽车冲压件材料利用率的方法
2018年09月10日
近几年随着人们生活水平的提高,汽车需求量也越来越大,各汽车厂的竞争日趋激烈,不断投入具备成本竞争力的新车型抢占市场,与此同时,用于生产汽车钢材所需的铁矿石与焦炭等自然资源却日趋紧张。提高材料利用率,不仅能降低汽车的制造成本,提高汽车品牌的竞争力,而且也符合节能降耗的环保理念。
工艺优化
落料排样优化,减少废料
针对一些异形的冲压件,可以对开卷落料模具内毛坯板料的排布方式进行优化,以减少废料,尽可能多的开卷出毛坯板料,提高材料利用率。
图1为T6车型的左右内纵梁落料模内毛坯板料的排样优化,将原先一步距产出一张板料,优化为一步距产出两张板料,减少了废料的重量,使得左右内纵梁的材料利用率从78.2%提升到87.6%。
材料规格合并,减少废料
为提高市场竞争力,丰富销售产品阵线,每年汽车厂都会有新车型的投入,新车型零件投入都会有新规格材料产生。当车型批量生产结束时,对应的专用钢材都会因消耗缓慢而占用库存,因此每增加一种新规格的钢材就会造成库存和管理成本的增加,汽车厂必须尽可能保证钢材的通用性,减少钢材的品种数量。
.jpg)
图1 排样优化对比图
.jpg)
图2 T6车型的机罩外板排样优化过程图
由于T6机罩的开卷步距与X7机罩卷料的料宽相近,通过现场验证,可以使用X7机罩的卷料,按步距1170mm的参数,用弧形摆剪生产T6机罩的板料。
通过工艺优化,材料利用率提高3.7%,同时减少原T6机罩外板专用的钢材规格,增加了材料的通用性,降低了库存与管理成本。
模具设计优化,一模多件
在一套模具上同时生产多个零件时,利用大零件孔洞处的废料生产一个或多个小零件,达到提高材料利用率的效果。
B5车型机罩内板和T7门内板的模具(图3),分别利用机罩内板和门内板零件孔洞处废料,冲压出机罩加强板零件和门锁加强板,避免了单独使用材料生产机罩加强板及门锁加强板。
.jpg)
图3 一模多件,套裁利用示意图
模具设计优化,板坯组合
模具设计时,将左右对称零件设计在一起冲压成形,通过工艺优化,将两张板料冲压出两个零件改为一张板料冲压出两个零件,减少工艺补充面积,提高材料利用率。
图4为MX3车型的左右后门外板零件模具设计与M44车型左右后门外板模具设计对比。MX3车型的左右后门外板一张板料冲压一个零件,零件的四个方向都需要工艺补充面;而M44车型左右后门外板为一张板料冲压出两个零件,相当于减少一个工艺补充面。通过对比,M44车型后门外板材料利用率比MX3后门外板材料利用率提高4.16%。
.jpg)
图4 模具设计对比图
材料尺寸优化
减小毛坯尺寸
通过调整毛坯板料在拉延模内的定位,减少拉延筋以外多余材料的工艺补充,从而减小零件所需的毛坯板料尺寸,提高材料的利用率。
图5为T/B车型前风窗下横梁零件,对拉延成形过渡件观察发现,拉延件的工艺补充区域还有很大一部分毛坯板料未被有效利用,通过测量,将此零件的开卷步距从原来的590mm减少到560mm,并对拉延模进行研合、对板料定位装置进行调整,经过外观检查和三坐标测量几何尺寸后确认:在板料步距减小30mm的情况下,零件成形正常,质量符合标准。
.jpg)
图5 T/B车型前风窗下横梁零件
T/B车型前风窗下横梁零件通过毛坯尺寸优化后,材料利用率提高2.4%。
控制卷料公差,增加毛坯数量
钢厂在生产钢卷和钢板时,对产品的厚度公差有一定的控制范围,表1为卷料尺寸控制标准。如果钢卷的厚度是按正公差交付到汽车厂,则开卷出来的毛坯板料厚度会在合格范围内偏厚,会造成毛坯板料和冲压零件的实际重量高于工艺定额重量,另一方面,会造成钢卷开卷出的实际板料数量少于理论数量,造成成材率降低。
例如R33顶盖零件,毛坯板料规格为0.8mm*1150mm*1680mm,材料牌号为DX54D+Z,其材料有三家供应商,三家供应商材料的公差尺寸均在合格范围内,但通过跟踪,其中一家材料每次开卷后的实际板料数量均少于理论数量,而另外两家钢卷材料开卷后的实际板料数量均略高于理论数量。
R33顶盖零件的工艺消耗定额为11.993kg。一个10t重的钢卷理论上可以开卷出R33顶盖板料为10000kg/11.993kg=834张。按照表1标准,R33顶盖零件使用的DX54D+Z材料的屈服强度小于280MPa,卷料宽度为1150mm,小于1200mm,因此最薄与最厚的板料厚度差异为0.06mm,则一个10t的钢卷最多和最少可以开卷出的板料张数分别为996张和771张,差异为125张,在采用负公差交货的情况下,相比正公差交货提高了15%的材料利用率。因此要求钢厂对钢卷采用负公差交货,可以显著增加毛坯数量,提高材料利用率。
废料收集再利用
部分零件在开卷落料时,会产生未利用的面积较大的废料,将这些废料用于汽车车身上其他小零件的生产,可以避免小零件所用材料的单独采购,节约了成本,同时也提高了整车的材料利用率。
表1 卷料尺寸控制标准
.jpg)
图6为R33后翼子板内板板料,其卷料规格为0.7mm *1275mm,开卷时存在废料。前围上盖板零件的板料尺寸为0.7mm*445mm*1070mm,消耗定额为2.594kg,这两个零件的材料牌号一致,通过收集R33后翼子板开卷步距的废料用于生产前围上盖板零件,材料利用率提高13%。
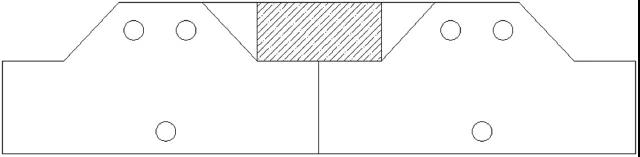
图6 R33后翼子板内板板料
通过类似方法收集R33侧围外板废料,其卷料规格为0.85mm*1450mm,材料牌号为DX56D+Z。R33左右后轮罩前部零件,尺寸为0.8mm*930mm*254mm,材料牌号为DX56D+Z。
通过收集R33侧围开卷时产生的废料,并对废料进行人工修剪,得到的矩形板料可用于生产R33左右后轮罩零件,材料利用率提高8%。
挺高卷料重量,减少头尾浪费
冲压工艺流程为材料供应商以带包装的卷料供货,卷料拆包后通过开卷设备剪切成冲压所需的各种形状板料,然后冲压出各种零件。开卷时需要对卷料外圈、内圈剪切处理,同时卷料头尾需要穿过开卷设备,每卷材料头尾约15米左右为生产正常损耗。因此开卷批量越大,卷料平均重量越重,开卷效率越高,卷料的平均损耗越少。
某车型整体侧围外板材料单车消耗60kg左右,冲压开卷线批量大,跟踪其侧围材料卷料重量,卷重分布范围为7t至15t,平均重量约10t,经过测算分析,如果将卷料重量提高到18吨,开卷线每批次将少生产一个卷料,即少一个卷料的料头料尾处理,侧围材料利用率可以提高约1%,开卷效率提高5%左右。结合设备能力,运输条件,向钢厂提出卷料重量要求,目前此侧围材料平均卷重18.5t,卷料转化为板料的利用率由原来的98.2%提高至99.2%(板料转化率=卷料净重/消耗定额×100%)。
结论
对冲压件而言,同一零件的材料利用率反映出工艺水平和技术水平的高低,本文结合冲压现场实际应用,从工艺优化、材料尺寸优化、废料再利用、卷料重量提高等方面介绍了提高汽车冲压件材料利用率的方法,通过上述方法的实际应用,提高了工艺、技术水平,为后续项目的工艺设计提供了参考依据。
提高材料利用率的方法很多,更多的方法需要通过实践验证,例如冲压覆盖件下料时,将现有的直线刀或圆弧刀改为波浪刀,通过改变板坯的形状,缩短板坯长度,从而提高材料利用率,此方法需要核算模具的投资、维修成本与提高材料利用率后的收益关系。总之,提高材料利用率是为了降低整车的完全成本,在做提高材料利用率方案时需要结合车型产量,考虑投资成本与收益的关系。
内容来自网络
AMTS 2019 第十五届上海国际汽车制造技术与装备及材料展览会将于2019年7月3-6日在上海举行,将汇聚来自中国/亚洲的知名汽车制造商和一级供应商的工程技术人员和决策者到场参观,预计将有来自世界各地800家展商参展,吸引80,000专业观众到场参观。
点击此处,申请2019展位
获取更多展会信息:
邮箱:info@for-expo.com
电话:86-21-6468 1300/6468 1550
工艺优化
落料排样优化,减少废料
针对一些异形的冲压件,可以对开卷落料模具内毛坯板料的排布方式进行优化,以减少废料,尽可能多的开卷出毛坯板料,提高材料利用率。
图1为T6车型的左右内纵梁落料模内毛坯板料的排样优化,将原先一步距产出一张板料,优化为一步距产出两张板料,减少了废料的重量,使得左右内纵梁的材料利用率从78.2%提升到87.6%。
材料规格合并,减少废料
为提高市场竞争力,丰富销售产品阵线,每年汽车厂都会有新车型的投入,新车型零件投入都会有新规格材料产生。当车型批量生产结束时,对应的专用钢材都会因消耗缓慢而占用库存,因此每增加一种新规格的钢材就会造成库存和管理成本的增加,汽车厂必须尽可能保证钢材的通用性,减少钢材的品种数量。
.jpg)
图1 排样优化对比图
.jpg)
图2 T6车型的机罩外板排样优化过程图
由于T6机罩的开卷步距与X7机罩卷料的料宽相近,通过现场验证,可以使用X7机罩的卷料,按步距1170mm的参数,用弧形摆剪生产T6机罩的板料。
通过工艺优化,材料利用率提高3.7%,同时减少原T6机罩外板专用的钢材规格,增加了材料的通用性,降低了库存与管理成本。
模具设计优化,一模多件
在一套模具上同时生产多个零件时,利用大零件孔洞处的废料生产一个或多个小零件,达到提高材料利用率的效果。
B5车型机罩内板和T7门内板的模具(图3),分别利用机罩内板和门内板零件孔洞处废料,冲压出机罩加强板零件和门锁加强板,避免了单独使用材料生产机罩加强板及门锁加强板。
.jpg)
图3 一模多件,套裁利用示意图
模具设计优化,板坯组合
模具设计时,将左右对称零件设计在一起冲压成形,通过工艺优化,将两张板料冲压出两个零件改为一张板料冲压出两个零件,减少工艺补充面积,提高材料利用率。
图4为MX3车型的左右后门外板零件模具设计与M44车型左右后门外板模具设计对比。MX3车型的左右后门外板一张板料冲压一个零件,零件的四个方向都需要工艺补充面;而M44车型左右后门外板为一张板料冲压出两个零件,相当于减少一个工艺补充面。通过对比,M44车型后门外板材料利用率比MX3后门外板材料利用率提高4.16%。
.jpg)
图4 模具设计对比图
材料尺寸优化
减小毛坯尺寸
通过调整毛坯板料在拉延模内的定位,减少拉延筋以外多余材料的工艺补充,从而减小零件所需的毛坯板料尺寸,提高材料的利用率。
图5为T/B车型前风窗下横梁零件,对拉延成形过渡件观察发现,拉延件的工艺补充区域还有很大一部分毛坯板料未被有效利用,通过测量,将此零件的开卷步距从原来的590mm减少到560mm,并对拉延模进行研合、对板料定位装置进行调整,经过外观检查和三坐标测量几何尺寸后确认:在板料步距减小30mm的情况下,零件成形正常,质量符合标准。
.jpg)
图5 T/B车型前风窗下横梁零件
T/B车型前风窗下横梁零件通过毛坯尺寸优化后,材料利用率提高2.4%。
控制卷料公差,增加毛坯数量
钢厂在生产钢卷和钢板时,对产品的厚度公差有一定的控制范围,表1为卷料尺寸控制标准。如果钢卷的厚度是按正公差交付到汽车厂,则开卷出来的毛坯板料厚度会在合格范围内偏厚,会造成毛坯板料和冲压零件的实际重量高于工艺定额重量,另一方面,会造成钢卷开卷出的实际板料数量少于理论数量,造成成材率降低。
例如R33顶盖零件,毛坯板料规格为0.8mm*1150mm*1680mm,材料牌号为DX54D+Z,其材料有三家供应商,三家供应商材料的公差尺寸均在合格范围内,但通过跟踪,其中一家材料每次开卷后的实际板料数量均少于理论数量,而另外两家钢卷材料开卷后的实际板料数量均略高于理论数量。
R33顶盖零件的工艺消耗定额为11.993kg。一个10t重的钢卷理论上可以开卷出R33顶盖板料为10000kg/11.993kg=834张。按照表1标准,R33顶盖零件使用的DX54D+Z材料的屈服强度小于280MPa,卷料宽度为1150mm,小于1200mm,因此最薄与最厚的板料厚度差异为0.06mm,则一个10t的钢卷最多和最少可以开卷出的板料张数分别为996张和771张,差异为125张,在采用负公差交货的情况下,相比正公差交货提高了15%的材料利用率。因此要求钢厂对钢卷采用负公差交货,可以显著增加毛坯数量,提高材料利用率。
废料收集再利用
部分零件在开卷落料时,会产生未利用的面积较大的废料,将这些废料用于汽车车身上其他小零件的生产,可以避免小零件所用材料的单独采购,节约了成本,同时也提高了整车的材料利用率。
表1 卷料尺寸控制标准
.jpg)
图6为R33后翼子板内板板料,其卷料规格为0.7mm *1275mm,开卷时存在废料。前围上盖板零件的板料尺寸为0.7mm*445mm*1070mm,消耗定额为2.594kg,这两个零件的材料牌号一致,通过收集R33后翼子板开卷步距的废料用于生产前围上盖板零件,材料利用率提高13%。
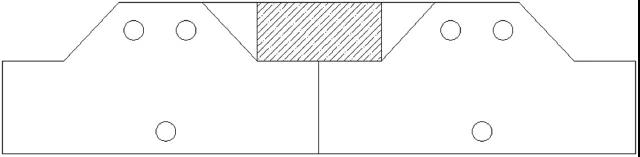
图6 R33后翼子板内板板料
通过类似方法收集R33侧围外板废料,其卷料规格为0.85mm*1450mm,材料牌号为DX56D+Z。R33左右后轮罩前部零件,尺寸为0.8mm*930mm*254mm,材料牌号为DX56D+Z。
通过收集R33侧围开卷时产生的废料,并对废料进行人工修剪,得到的矩形板料可用于生产R33左右后轮罩零件,材料利用率提高8%。
挺高卷料重量,减少头尾浪费
冲压工艺流程为材料供应商以带包装的卷料供货,卷料拆包后通过开卷设备剪切成冲压所需的各种形状板料,然后冲压出各种零件。开卷时需要对卷料外圈、内圈剪切处理,同时卷料头尾需要穿过开卷设备,每卷材料头尾约15米左右为生产正常损耗。因此开卷批量越大,卷料平均重量越重,开卷效率越高,卷料的平均损耗越少。
某车型整体侧围外板材料单车消耗60kg左右,冲压开卷线批量大,跟踪其侧围材料卷料重量,卷重分布范围为7t至15t,平均重量约10t,经过测算分析,如果将卷料重量提高到18吨,开卷线每批次将少生产一个卷料,即少一个卷料的料头料尾处理,侧围材料利用率可以提高约1%,开卷效率提高5%左右。结合设备能力,运输条件,向钢厂提出卷料重量要求,目前此侧围材料平均卷重18.5t,卷料转化为板料的利用率由原来的98.2%提高至99.2%(板料转化率=卷料净重/消耗定额×100%)。
结论
对冲压件而言,同一零件的材料利用率反映出工艺水平和技术水平的高低,本文结合冲压现场实际应用,从工艺优化、材料尺寸优化、废料再利用、卷料重量提高等方面介绍了提高汽车冲压件材料利用率的方法,通过上述方法的实际应用,提高了工艺、技术水平,为后续项目的工艺设计提供了参考依据。
提高材料利用率的方法很多,更多的方法需要通过实践验证,例如冲压覆盖件下料时,将现有的直线刀或圆弧刀改为波浪刀,通过改变板坯的形状,缩短板坯长度,从而提高材料利用率,此方法需要核算模具的投资、维修成本与提高材料利用率后的收益关系。总之,提高材料利用率是为了降低整车的完全成本,在做提高材料利用率方案时需要结合车型产量,考虑投资成本与收益的关系。
内容来自网络
AMTS 2019 第十五届上海国际汽车制造技术与装备及材料展览会将于2019年7月3-6日在上海举行,将汇聚来自中国/亚洲的知名汽车制造商和一级供应商的工程技术人员和决策者到场参观,预计将有来自世界各地800家展商参展,吸引80,000专业观众到场参观。
点击此处,申请2019展位
获取更多展会信息:
邮箱:info@for-expo.com
电话:86-21-6468 1300/6468 1550