行业新闻
汽车先进高强钢成形技术应用现状及发展趋势
2018年09月06日
随着能源和环境问题的日益突出以及人们对汽车安全性能关注度的持续增加,在保证安全的前提下实现车身的轻量化正成为汽车工业的主要发展方向。在降低油耗、减少排放的诸多措施中,减轻车重的效果是非常明显的。
钢铁、铝材和塑料是制造汽车的三大材料,其中钢铁是汽车车体的主要材料,也是性价比最高的材料,而先进高强钢作为一种优秀的车用轻量化材料,其发展和应用为节能减排提供了重要途径。采用先进高强度钢板,可以在达到强度要求的同时,有效减少冲压件厚度和数量,从而达到减重的目的;另一方面,采用高强度钢板更容易达到安全性能指标要求。在白车身制造方面,近年来高强钢板的应用及使用比例在不断提高。
目前的冷冲压工艺在对高强度钢板进行成形的方面存在着明显的不足,易产生开裂、回弹等缺陷,无法满足产品的要求。热成形技术作为一种新型的成形工艺,可以有效地弥补高强度钢板的成形缺陷,它具有成形能力高、零件回弹小、成形零件强度级别高的优点,目前已广泛应用于全球各大汽车公司的多种车型,重点使用在对碰撞要求较高的部位,如图1所示的汽车门槛、前保险杠横梁、B柱等。
汽车先进高强钢在白车身上的应用现状
近年来,国内外企业开始不断研究并开发各种先进高强钢。国际钢铁协会先进高强钢应用指南第三版中,将高强钢分为传统高强钢和先进高强钢。传统高强钢主要包括碳锰钢、烘烤硬化钢、高强度无间隙原子钢和高强度低合金钢,先进高强钢主要包括双相钢、相变诱发塑性钢、马氏体钢、复相钢、热成形钢和孪晶诱发塑性钢。
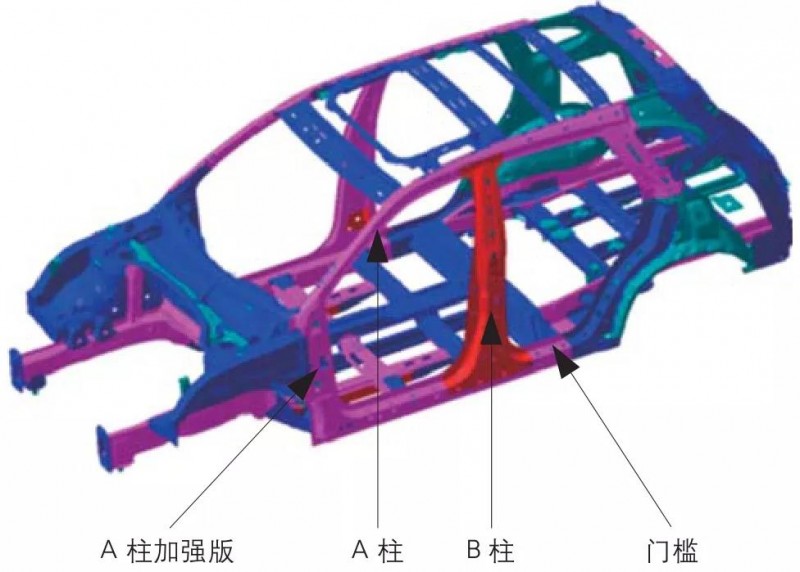
图1 高强度钢板在汽车上的应用
传统的高强钢多是通过固溶、析出和细化晶粒作为主要强化手段,而先进高强钢是指通过相变进行强化的钢种,组织中含有马氏体、贝氏体和残余奥氏体。汽车用先进高强钢分为热轧、冷轧和热镀锌产品,其工艺特点都是通过相变实现强化的。
先进高强钢的强度(500~1500MPa)和塑性配合优于普通高强钢,同时具有高强度和较好的成形性,特别是加工硬化指数较高,有利于提高冲撞过程中的能量吸收,所以其在减重和安全性方面具有双重优势。
汽车先进高强钢在国外的应用现状
纵观汽车厂在高强钢使用方面的发展,宝马汽车在欧美地区发展速度是较快的。宝马5系列在不同年代上市的汽车,用料的平均最小屈服强度从1998年版的198MPa增加到2012年版的415MPa,屈服强度在500MPa的高强钢的使用比例也大幅度增加,宝马旗下Z4高强钢板应用比例高达55%,而2009款宝马5系车型从62.1%的比例,提高到了2010年的72%。
日本在高强度汽车板生产和使用方面有明显优势,日本早在1997年就启动了“超级钢铁材料”的国家研究计划,为期10年,其主要目的是实现钢铁材料的强度翻番,寿命翻番。日本钢铁工程控股公司(JFE)在2015年开发出具有良好延展性和扩孔性的980MPa级高级冷轧钢板,在业界属于首例。目前日本政府主导的科研项目“创新型结构材料研发”中的子项目“超高张力钢材开发”进展顺利,其目标是在2020年前开发出抗拉强度1.5GPa和延伸率20%的超高强度钢板,目前项目中期目标抗拉强度1.2GPa和延伸率15%的超高强度钢板已经在实验室试制成功。另外,美国的通用公司,2004年高强钢的使用率大幅度上升,低碳钢的使用率减少至40%,先进高强钢使用率达到12%,2006年先进高强钢的使用率已至18%。2016年通用公司旗下全新一代君越车身高强度钢材比例达到了41%,在A柱、B柱、门槛梁等核心区域,屈服强度在900~1500MPa的超高强钢和热成形钢大量被应用。
先进高强钢在世界范围内已经得到了一定的应用,并显示出在减重、安全和环保方面的优势。有理由相信,其将成为汽车减重的主要材料。
汽车先进高强钢在国内的应用现状
汽车工业的发展、汽车产量和汽车保有量的增加,在给人们出行带来方便的同时,也产生了油耗、安全和环保三大问题。为保证汽车工业的健康发展,各国制定了相应的法规,而各国汽车工业界认为,满足各项法规要求较为有效的手段是采用高强度轻量化材料。先进高强钢其最大的优势就是:提高材料的强度,在所要求的性能不变或略有提高的前提下,减薄板材构件的厚度,从而降低构件的质量。
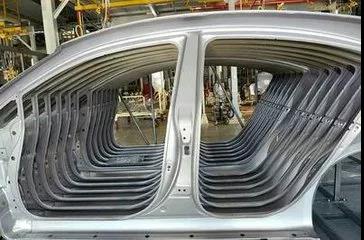
目前,国内传统高强钢的品种和质量与国外的差距不大,相应的国家标准已由宝钢负责制定完成。但是先进高强钢与欧美等发达国家和地区还有一定差距,使用的标准也主要是由这些国家制定。近几年,我国汽车工业的发展非常迅猛,整体技术水平有了很大的提高,先进高强钢的应用也大幅度增加,有利地促进了国内先进高强钢的开发和生产。目前,宝钢、鞍钢、马钢等主要钢铁企业都在积极开发先进高强钢。其中宝钢经过多年的发展,已经迅速崛起为中国热冲压领域的先驱者。目前,宝钢已经基本掌握了热冲压系列核心技术,实现了阶段性的跨越式发展。2007年年底,上海宝钢热冲压零部件有限公司正式成立。2008年上半年,宝钢建成了以研发为主兼顾小批量生产的第一条热冲压生产线。2009年9月,宝钢第二条热冲压生产线建成投产,开发的抗拉强度为1200MPa和1500MPa的热冲压成形钢,已经大量生产供货。至今,宝钢已经实现向江淮、华晨、奇瑞等汽车厂小批量供货,用其生产的热冲压零件的尺寸精度和力学性能均已达到行业先进水平。近几年,宝钢正开发抗拉强度高达1800MPa的热冲压成形钢。
先进高强钢成形方法简介
减薄和高强是先进高强钢在减重和安全方面的优势,但也对冲压成形工艺提出了新的挑战。这两个优势对冲压工艺而言是恶化成形性的双重因素,使车身零件在成形过程中易开裂和产生过量回弹,冲压件的回弹常用U形件的拉深试验来测定。相对于软钢和传统高强钢,先进高强钢的回弹更大,且难以控制,特别是当钢板初始强度大于1000MPa时,传统的冷冲压方法就难以生产结构、形状较复杂的车身零件,这就需要合适的解决方法。
为解决这一难题,热冲压技术应运而生。热成形工艺就是利用金属在高温状态下塑性和延展性会迅速增加、屈服强度迅速下降的特点,通过模具使零件成形的工艺。通过对特殊的高强度钢板加热到900℃左右,使之易于拉延成形,再经过速冷,使钢板抗拉强度达到1500MPa左右,从而达到零件对超高强度的要求。热成形工艺流程为:落料--加热至奥氏体状态并保温--快速放入模具中冲压成形--保压定形并淬火--激光切边、割孔--去氧化皮--涂油(防锈处理)。
先进高强钢的热冲压技术,主要是同济大学、哈尔滨工业大学、吉林大学和宝钢等相关单位在对热冲压技术、关键设备进行研究。国内大学研究高强度汽车板热冲压工艺,取得成果较多的是同济大学机械与材料学院,主要对热冲压过程中,钢板的加热温度与钢板内部组织结构变化模式、冲压速度、保压时间、淬火速度、冲压模具温度变化等对成形的影响进行模拟研究。
先进高强钢在白车身开发中的应用及发展前景
由于汽车未来的市场需求,钢厂应具备制造1000MPa级及以上高强钢的能力才能适应未来市场的需求,才能在减重、节能、提高安全性、降低排放等方面展现出良好的应用前景和好的竞争力。但随着先进高强钢的大量应用,与过去采用大量软钢相比,成形中的起皱、回弹、模具损伤、开裂、翘曲等成形问题和困难大量出现。因此,完善其成形技术也是下一阶段先进高强钢研发及应用的主要研究任务。
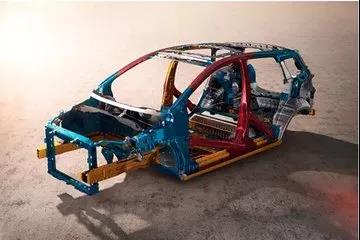
我国先进高强钢的研发现状及发展趋势主要如下
⑴ 热冲压材料的开发。目前国内各大钢铁公司均在进行先进高强钢的生产和研究,其中最具代表性的企业主要有宝钢、鞍钢、马钢等,主要进行强度在1800MPa级及以上的热冲压材料开发,同时要在现有强度级别下进一步提升其延伸率,以满足强度及碰撞要求。
⑵ 防腐蚀性。先进高强钢在强度和成形性方面展示了良好的应用前景,但是在现代汽车工业中,不仅要采用高强度和先进高强度钢,同时为保证汽车的防腐蚀性能,还应该加大镀层板的研究和产业化,并提高镀层板的品种和质量来提高先进高强钢材料的抗腐蚀性。
⑶ 研究先进高强钢的热冲压成形防止回弹技术。材料特性决定了其成形工艺,材料的强度越高,成形后零件的回弹越大,防止这种成形缺陷的技术难度越大,先进的成形方法尤其是防回弹技术是未来的主要研究方向之一。
⑷ 新型热成形模具钢材料的研究开发。为了有效提高模具热传导和抗拉毛特性,增加模具的使用寿命,提高生产节拍,亟需研究出高导热、高耐磨、高韧性的热冲压模具钢材料。
⑸ 先进高强钢热冲压成形的模具设计技术。在冲压过程中要使升温、保温与降温过程模具内温度尽量均匀,防止热应力过高而引起模具的损坏;同时要研究热成形模具模内淬火分析和疲劳寿命预测分析技术,另外冲压设备的选择匹配也是模具设计的难点。
⑹ 先进高强钢热冲压成形计算机模拟技术研究。需要解决的关键问题是将先进高强钢准确的材料本构模型嵌入到数值模拟软件中,进而进一步研究高强钢的热成形有限元数值模拟建模技术。
内容来自网络
钢铁、铝材和塑料是制造汽车的三大材料,其中钢铁是汽车车体的主要材料,也是性价比最高的材料,而先进高强钢作为一种优秀的车用轻量化材料,其发展和应用为节能减排提供了重要途径。采用先进高强度钢板,可以在达到强度要求的同时,有效减少冲压件厚度和数量,从而达到减重的目的;另一方面,采用高强度钢板更容易达到安全性能指标要求。在白车身制造方面,近年来高强钢板的应用及使用比例在不断提高。
目前的冷冲压工艺在对高强度钢板进行成形的方面存在着明显的不足,易产生开裂、回弹等缺陷,无法满足产品的要求。热成形技术作为一种新型的成形工艺,可以有效地弥补高强度钢板的成形缺陷,它具有成形能力高、零件回弹小、成形零件强度级别高的优点,目前已广泛应用于全球各大汽车公司的多种车型,重点使用在对碰撞要求较高的部位,如图1所示的汽车门槛、前保险杠横梁、B柱等。
汽车先进高强钢在白车身上的应用现状
近年来,国内外企业开始不断研究并开发各种先进高强钢。国际钢铁协会先进高强钢应用指南第三版中,将高强钢分为传统高强钢和先进高强钢。传统高强钢主要包括碳锰钢、烘烤硬化钢、高强度无间隙原子钢和高强度低合金钢,先进高强钢主要包括双相钢、相变诱发塑性钢、马氏体钢、复相钢、热成形钢和孪晶诱发塑性钢。
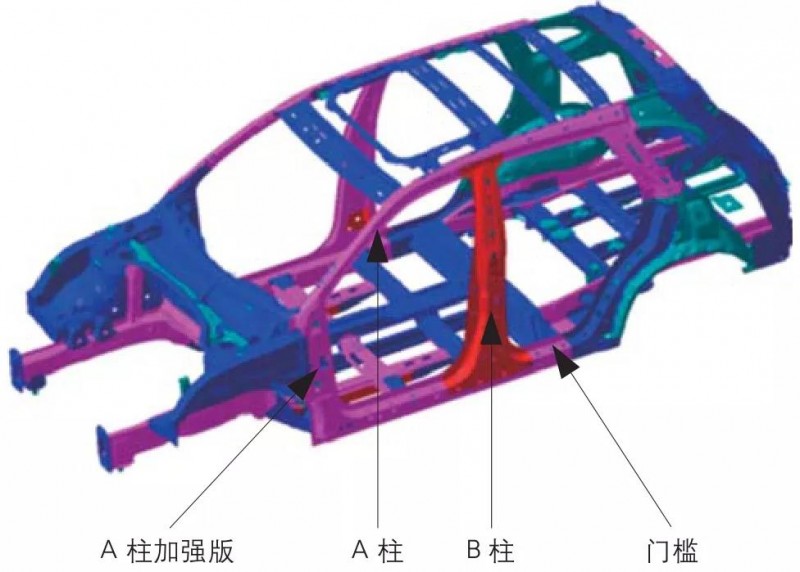
图1 高强度钢板在汽车上的应用
传统的高强钢多是通过固溶、析出和细化晶粒作为主要强化手段,而先进高强钢是指通过相变进行强化的钢种,组织中含有马氏体、贝氏体和残余奥氏体。汽车用先进高强钢分为热轧、冷轧和热镀锌产品,其工艺特点都是通过相变实现强化的。
先进高强钢的强度(500~1500MPa)和塑性配合优于普通高强钢,同时具有高强度和较好的成形性,特别是加工硬化指数较高,有利于提高冲撞过程中的能量吸收,所以其在减重和安全性方面具有双重优势。
汽车先进高强钢在国外的应用现状
纵观汽车厂在高强钢使用方面的发展,宝马汽车在欧美地区发展速度是较快的。宝马5系列在不同年代上市的汽车,用料的平均最小屈服强度从1998年版的198MPa增加到2012年版的415MPa,屈服强度在500MPa的高强钢的使用比例也大幅度增加,宝马旗下Z4高强钢板应用比例高达55%,而2009款宝马5系车型从62.1%的比例,提高到了2010年的72%。
日本在高强度汽车板生产和使用方面有明显优势,日本早在1997年就启动了“超级钢铁材料”的国家研究计划,为期10年,其主要目的是实现钢铁材料的强度翻番,寿命翻番。日本钢铁工程控股公司(JFE)在2015年开发出具有良好延展性和扩孔性的980MPa级高级冷轧钢板,在业界属于首例。目前日本政府主导的科研项目“创新型结构材料研发”中的子项目“超高张力钢材开发”进展顺利,其目标是在2020年前开发出抗拉强度1.5GPa和延伸率20%的超高强度钢板,目前项目中期目标抗拉强度1.2GPa和延伸率15%的超高强度钢板已经在实验室试制成功。另外,美国的通用公司,2004年高强钢的使用率大幅度上升,低碳钢的使用率减少至40%,先进高强钢使用率达到12%,2006年先进高强钢的使用率已至18%。2016年通用公司旗下全新一代君越车身高强度钢材比例达到了41%,在A柱、B柱、门槛梁等核心区域,屈服强度在900~1500MPa的超高强钢和热成形钢大量被应用。
先进高强钢在世界范围内已经得到了一定的应用,并显示出在减重、安全和环保方面的优势。有理由相信,其将成为汽车减重的主要材料。
汽车先进高强钢在国内的应用现状
汽车工业的发展、汽车产量和汽车保有量的增加,在给人们出行带来方便的同时,也产生了油耗、安全和环保三大问题。为保证汽车工业的健康发展,各国制定了相应的法规,而各国汽车工业界认为,满足各项法规要求较为有效的手段是采用高强度轻量化材料。先进高强钢其最大的优势就是:提高材料的强度,在所要求的性能不变或略有提高的前提下,减薄板材构件的厚度,从而降低构件的质量。
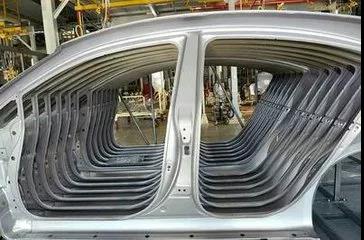
目前,国内传统高强钢的品种和质量与国外的差距不大,相应的国家标准已由宝钢负责制定完成。但是先进高强钢与欧美等发达国家和地区还有一定差距,使用的标准也主要是由这些国家制定。近几年,我国汽车工业的发展非常迅猛,整体技术水平有了很大的提高,先进高强钢的应用也大幅度增加,有利地促进了国内先进高强钢的开发和生产。目前,宝钢、鞍钢、马钢等主要钢铁企业都在积极开发先进高强钢。其中宝钢经过多年的发展,已经迅速崛起为中国热冲压领域的先驱者。目前,宝钢已经基本掌握了热冲压系列核心技术,实现了阶段性的跨越式发展。2007年年底,上海宝钢热冲压零部件有限公司正式成立。2008年上半年,宝钢建成了以研发为主兼顾小批量生产的第一条热冲压生产线。2009年9月,宝钢第二条热冲压生产线建成投产,开发的抗拉强度为1200MPa和1500MPa的热冲压成形钢,已经大量生产供货。至今,宝钢已经实现向江淮、华晨、奇瑞等汽车厂小批量供货,用其生产的热冲压零件的尺寸精度和力学性能均已达到行业先进水平。近几年,宝钢正开发抗拉强度高达1800MPa的热冲压成形钢。
先进高强钢成形方法简介
减薄和高强是先进高强钢在减重和安全方面的优势,但也对冲压成形工艺提出了新的挑战。这两个优势对冲压工艺而言是恶化成形性的双重因素,使车身零件在成形过程中易开裂和产生过量回弹,冲压件的回弹常用U形件的拉深试验来测定。相对于软钢和传统高强钢,先进高强钢的回弹更大,且难以控制,特别是当钢板初始强度大于1000MPa时,传统的冷冲压方法就难以生产结构、形状较复杂的车身零件,这就需要合适的解决方法。
为解决这一难题,热冲压技术应运而生。热成形工艺就是利用金属在高温状态下塑性和延展性会迅速增加、屈服强度迅速下降的特点,通过模具使零件成形的工艺。通过对特殊的高强度钢板加热到900℃左右,使之易于拉延成形,再经过速冷,使钢板抗拉强度达到1500MPa左右,从而达到零件对超高强度的要求。热成形工艺流程为:落料--加热至奥氏体状态并保温--快速放入模具中冲压成形--保压定形并淬火--激光切边、割孔--去氧化皮--涂油(防锈处理)。
先进高强钢的热冲压技术,主要是同济大学、哈尔滨工业大学、吉林大学和宝钢等相关单位在对热冲压技术、关键设备进行研究。国内大学研究高强度汽车板热冲压工艺,取得成果较多的是同济大学机械与材料学院,主要对热冲压过程中,钢板的加热温度与钢板内部组织结构变化模式、冲压速度、保压时间、淬火速度、冲压模具温度变化等对成形的影响进行模拟研究。
先进高强钢在白车身开发中的应用及发展前景
由于汽车未来的市场需求,钢厂应具备制造1000MPa级及以上高强钢的能力才能适应未来市场的需求,才能在减重、节能、提高安全性、降低排放等方面展现出良好的应用前景和好的竞争力。但随着先进高强钢的大量应用,与过去采用大量软钢相比,成形中的起皱、回弹、模具损伤、开裂、翘曲等成形问题和困难大量出现。因此,完善其成形技术也是下一阶段先进高强钢研发及应用的主要研究任务。
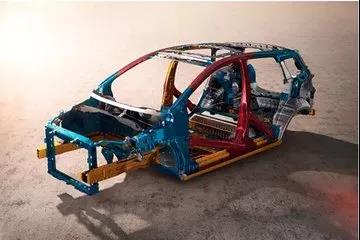
我国先进高强钢的研发现状及发展趋势主要如下
⑴ 热冲压材料的开发。目前国内各大钢铁公司均在进行先进高强钢的生产和研究,其中最具代表性的企业主要有宝钢、鞍钢、马钢等,主要进行强度在1800MPa级及以上的热冲压材料开发,同时要在现有强度级别下进一步提升其延伸率,以满足强度及碰撞要求。
⑵ 防腐蚀性。先进高强钢在强度和成形性方面展示了良好的应用前景,但是在现代汽车工业中,不仅要采用高强度和先进高强度钢,同时为保证汽车的防腐蚀性能,还应该加大镀层板的研究和产业化,并提高镀层板的品种和质量来提高先进高强钢材料的抗腐蚀性。
⑶ 研究先进高强钢的热冲压成形防止回弹技术。材料特性决定了其成形工艺,材料的强度越高,成形后零件的回弹越大,防止这种成形缺陷的技术难度越大,先进的成形方法尤其是防回弹技术是未来的主要研究方向之一。
⑷ 新型热成形模具钢材料的研究开发。为了有效提高模具热传导和抗拉毛特性,增加模具的使用寿命,提高生产节拍,亟需研究出高导热、高耐磨、高韧性的热冲压模具钢材料。
⑸ 先进高强钢热冲压成形的模具设计技术。在冲压过程中要使升温、保温与降温过程模具内温度尽量均匀,防止热应力过高而引起模具的损坏;同时要研究热成形模具模内淬火分析和疲劳寿命预测分析技术,另外冲压设备的选择匹配也是模具设计的难点。
⑹ 先进高强钢热冲压成形计算机模拟技术研究。需要解决的关键问题是将先进高强钢准确的材料本构模型嵌入到数值模拟软件中,进而进一步研究高强钢的热成形有限元数值模拟建模技术。
内容来自网络
AMTS 2019 第十五届上海国际汽车制造技术与装备及材料展览会将于2019年7月3-6日在上海举行,将汇聚来自中国/亚洲的知名汽车制造商和一级供应商的工程技术人员和决策者到场参观,预计将有来自世界各地800家展商参展,吸引80,000专业观众到场参观。
点击此处,申请2019展位
获取更多展会信息:
邮箱:info@for-expo.com
电话:86-21-6468 1300/6468 1550
点击此处,申请2019展位
获取更多展会信息:
邮箱:info@for-expo.com
电话:86-21-6468 1300/6468 1550