行业新闻
热喷涂技术在铝合金发动机中的应用
2017年08月31日
为减轻发动机重量、降低燃油消耗,实现节能减排,汽车制造商开发了在铝合金缸孔表面喷涂涂层取代传统镶嵌铸缸套的先进工艺。为推动缸孔喷涂技术在国内汽车市场的应用进程,本文对铝合金缸孔应用等离子喷涂工艺展开了研究及试验分析。
为了降低燃油消耗和CO2的排放,汽车的轻量化成为大家关注的焦点之一。国外的大众、奔驰和福特等公司采用在铝合金缸孔表面喷涂涂层的技术取代镶嵌铸缸套的工艺,以达到发动机减重、降低油耗和排放的目的,目前部分机型已达到量产水平,缸孔喷涂工艺已从研发阶段逐步进入实用化阶段,在发动机上的应用愈来愈为广泛。
为推动缸孔喷涂技术在国内汽车市场的应用进程,本文对等离子单丝喷涂工艺展开了研究及试验分析。
等离子单丝喷涂技术原理
金属丝材为阳极,钨极为阴极,阳极和阴极之间产生高频率电弧,等离子气体(氦、氢、氮或其混合气体)流经电极之间被电离,产生几厘米长的等离子火焰(中心温度可高达16 000℃)。喷涂丝材进给至等离子火焰中心被迅速加热到熔融状态,并在雾化高压气体(氮气或压缩空气)的作用下高速喷打在已毛化处理的缸孔内壁,形成0.3~0.5 mm厚的涂层,如图1所示。
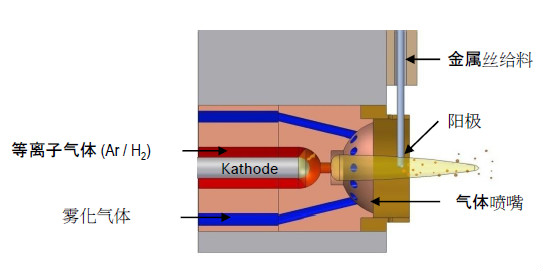
图1 等离子单丝喷涂原理
据资料显示,喷涂技术能够实现缸孔摩擦系数降低20%~30%、机油耗降低50%、燃油耗降低2%~4%以及CO2排放降低2%~4%的效果,同时可减轻发动机重量,并提高缸孔耐腐蚀能力。
等离子喷涂工艺流程
通过与国外喷涂厂家的交流,我们试制了喷涂缸体,掌握了等离子喷涂的工艺流程:缸孔精镗—缸孔毛化—清洗—缸孔喷涂—过喷涂处理—最终珩磨。在此,对喷涂工艺的关键工序(见图2)展开分析。
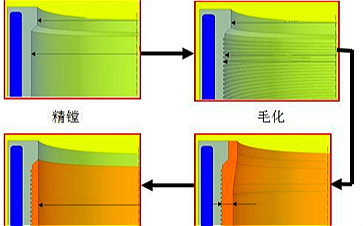
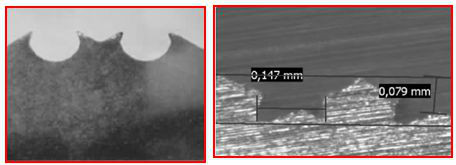
图2 喷涂工艺的关键工序
1.缸孔毛化
喷涂前需对缸孔内壁进行机械毛化,加工出类似燕尾槽的槽型,使涂层与内壁沟槽形成机械咬合,以提高涂层结合强度。图3所示为毛化刀具及加工槽型。
图3 刀具图片及加工槽型
毛化刀具主要由国外刀具供应商联合发动机厂家合作开发,均设有专利保护。目前已成功研发并成熟应用的刀具厂家包括玛帕、瓦尔特和钴领等。
2.缸孔清洗
毛化处理后必须对缸孔表面进行清洗,去除油污、碎屑及毛刺,保证缸孔内壁的清洁度以提高涂层与缸孔的结合强度。通常采用国产三工位清洗机即可满足要求:整体喷淋—缸孔定位清洗—压缩空气吹干。同时需在清洗工位后设置SPC检测站,对毛化后缸孔尺寸进行检测,主要检测内容为缸孔直径、位置度。
3.缸孔喷涂
(1)喷涂材料
根据产品性能要求的不同喷涂丝材也不尽相同,主要包括低碳钢、中碳钢、高碳钢以及不锈钢材料。具体分析如下:
① 低碳钢:成本最低,可实现喷涂涂层与常规活塞环的良好匹配;
② 中碳钢:喷涂涂层可改善缸孔耐磨性和抗腐蚀性,推荐采用氮化活塞环进行匹配;
③ 高碳钢:喷涂涂层具有很高的耐磨性,常用于柴油发动机;
④ 不锈钢:喷涂涂层具有极高的耐磨性及抗腐蚀性,常用于EGR技术发动机。
目前,国内材料供应体系已非常成熟,如北京矿冶研究总院、广州三鑫和佛山先进设备等公司。
(2)喷涂工艺
对于直径75mm、长度130mm的内孔,采用德国某公司的等离子单丝喷涂设备进行喷涂,材料为含碳量0.8%的碳钢丝材,喷涂工艺参数控制如表1所示。
表1 喷涂工艺参数控制
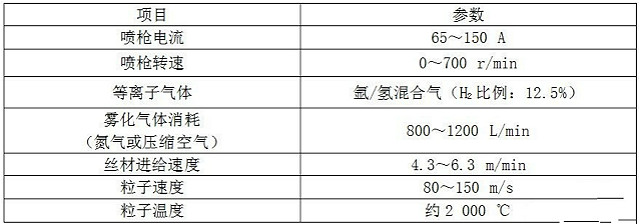
对喷涂后的涂层进行检测,获得如下数据:涂层硬度400~500 HV,较铸铁缸套硬度明显提高,耐磨性增强;涂层结合强度40~50 MPa,保证涂层在发动机运转过程中不会脱落;涂层厚度0.15 mm,大大低于铸铁缸套厚度,可实现缸体减重1.2 kg,且较薄的涂层也在一定程度上提高了缸孔导热性,降低发动机工作时气缸内壁的温度;同时由于涂层本身固有的微孔特性,可以增加储油量,配合涂层中含有的FeO、Fe3O4等氧化物(固体润滑剂),更好地保证了活塞环与缸套的润滑效果。资料显示,在戴姆勒某发动机上采用喷涂技术后摩擦功比原来铸铁缸套(30°网纹夹角)减少20%,机油消耗减少50%。
为确保喷涂过程的一致性,需对喷涂工艺参数进行在线监测,以确保涂层性能的稳定及可靠。在线监测主要参数为喷涂粒子的速度及温度,常用的检测设备有Tecnar公司的DPV eVOLUTION、Accuraspray G3C和Oseir公司的SprayWatch在线监测系统;SprayWatch在线监测系统采用数字成像技术原理,利用CCD 相机产生喷涂数字化影像,一次性捕捉34 mm×27 mm×25 mm 体积范围内的几千个小成像点,获取几百行列的有效信息。通过测量粒子飞行时间确定粒子速度,通过双色高温测量法测量粒子温度。
4.涂层珩磨
喷涂后的缸孔仍需采用珩磨工艺,以满足产品使用要求。针对涂层的材料和喷涂表面形状,涂层表面存在微小的波浪形貌,当涂层厚度控制在0.55 mm以内时,喷涂不会影响珩磨后的缸孔位置度,采用与现行铸铁缸套相同的浮动珩磨工艺即可满足珩磨要求。不同的是,需对珩磨条粒度、材质进行优化并调整相关珩磨参数,以保证喷涂涂层的珩磨要求。珩磨喷涂后的缸孔的工艺要求如表2所示。
表2 珩磨喷涂后的缸孔的工艺要求
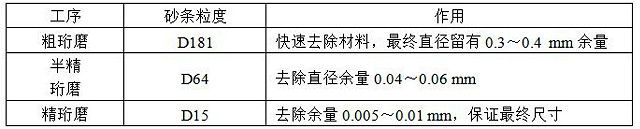
喷涂试验分析
采用等离子单丝喷涂技术,对某直径75 mm铝合金缸体喷涂高碳钢材料,并装配整机进行发动机台架验证。试验结果表明,缸孔涂层在经过400 h可靠性试验后涂层无拉缸、划伤和剥离等异常磨损现象;主要性能参数指标,如发动机功率、扭矩和活塞漏气量等,均满足标准要求。
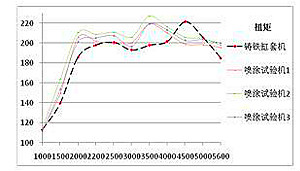
图4 发动机功率、扭矩曲线
从图4所示的功率、扭矩曲线可以看出,采用喷涂技术后,发动机功率、扭矩有明显提升,尤其是中低速扭矩提升幅度非常可观,最大提升约20 Nm(9%)。
结语
缸孔喷涂在发动机制造领域属于一种先进且成熟的技术。试验结果显示,铝合金缸孔喷涂技术可以替代镶嵌铸铁缸套工艺并满足发动机使用要求。为减少汽车排放,提高环境质量,在汽车电动技术尚未完全普及的情况下,在国内进行喷涂技术的转化及应用具有非常重大的意义。
部分内容来源:中国汽车材料网
作为亚洲最大的汽车材料与设计、工艺与装备、质量与装配、工程与服务技术行业盛会,上海国际汽车制造技术与装备及材料展览会(AMTS)自2004年创办以来,以国际化的视角呈现汽车工程领域全方位的系统集成解决方案。10多年来,展会的规模、展示范围以及专业观众快速增长,极大地推动了国际汽车制造装备技术交流及贸易的发展!
AMTS 2018第十四届上海国际汽车制造技术与装备及材料展览会将于2018年9月4-7日在上海举行,将汇聚来自中国/亚洲的知名汽车制造商和一级供应商的工程技术人员和决策者到场参观,预计将有来自世界各地800家展商参展,展示面积首次突破100,000平方米,吸引80,000专业观众到场参观。
立即点击申请AMTS 2018展位
获取更多AMTS 2018展会信息:
邮箱:info@for-expo.com
电话:86-21-6468 1300/6468 1550
2018年9月4-7日,上海新国际博览中心E1,E2,E3,E4,E5,E6,E7,N4,N5馆,我们不见不散。