行业新闻
感应加热技术工艺在汽车制造中的应用
2018年05月03日
一、感应加热的原理及特点
1. 电磁感应现象
电磁感应现象是指放在变化磁通量中的导体,会产生电动势。此电动势称为感应电动势或感生电动势,若将此导体闭合成一回路,则该电动势会驱使电子流动,形成感应电流(见图1)。
.jpg)
电磁感应现象的发现,乃是电磁学领域中最伟大的成就之一。它不仅揭示了电与磁之间的内在联系,而且为电与磁之间的相互转化奠定了实验基础,为人类获取巨大而廉价的电能开辟了道路,在实用上有重大意义。电磁感应现象的发现,标志着一场重大的工业和技术革命的到来。事实证明,电磁感应是发电机、感应电机、变压器和大部分其他电力设备操作的基础,在电工、电子技术、电气化、自动化和工业加热方面的广泛应用,对推动社会生产力和科学技术的发展起到了重要的作用。
2. 感应加热原理
感应加热技术应用的就是变压器的工作原理,在感应器(变压器的初级线圈)中通入交变电流后,在其周围会产生交变磁场,放置在其附近的金属工件(变压器的短路次级线圈)在交变磁场的作用下,会产生电动势,在该电动势的驱使下使工件中的电子流动形成感应电流(涡流见图2)。在工件中电阻的作用下将电能转变为热能,使工件本身加热。
.jpg)
3. 感应加热的优点
如上所述,感应加热是利用在金属中产生的感应电流直接实现工件的加热。该加热方式是一种非接触式加热,其电热转换效率主要取决于金属材料的磁导率和感应器(变压器的初级线圈)与工件(变压器的次级线圈)的耦合程度,即金属的磁导率越高,热转换效率越高,感应器与工件的耦合越紧,热转换效率越高。而普通的炉中加热均需要有加热源,通过加热源的辐射、热量在加热介质中的对流,以及被加热体的热传导三个过程实现金属工件的加热,其加热效率是加热源的能量转换效率、热量的对流效率和热量在被加热体中的传导效率的综合效率。相比之下,感应加热具有如下优点:
(1) 没有对流和传导的加热过程,在工件的内部直接加热,加热速度快。
(2)减少了工件在加热过程中的氧化和脱碳。
(3) 节约能源,不需要炉中加热时所需的加热炉的预热和升温,可随时开始和停止加热,在非工作周期不需要保持加热炉的温度。
(4)加热时间短,生产效率高,有效地减少了工艺成本。
(5)可实现零件的局部加热。
(6)设备的机械化、自动化程度高,占地面积少,可实现与自动化生产线的共线生产。
(7)工作环境清洁、安全、噪声小,属于环境友好型生产方式。
(8)设备的故障率低,维护、维修、保养成本低。
2感应加热新技术及新工艺在汽车制造领域中的应用
由于感应加热技术具有上述诸多优点,在现代汽车制造中广泛用于铸造加工中的黑色金属及各种有色金属的熔炼,压力加工中的毛坯透热,零件热处理中的淬火、回火、正火及退火,焊接加工中的焊前预热、焊后的焊缝去应力退火、有色金属的钎焊,部件装配过程中过盈配合零件的热装配、金属制件与塑料件的热合成,粘接涂胶过程中的感应加热烘干及固化,以及表面防护中的非金属粉末热涂覆等。
1. 隧道式感应加热炉的应用
在汽车零部件铸件的生产过程中,由美国Aj a xTOCCO、Inductotherm Group、德国INDUGA等世界着名感应加热设备制造商所提供技术先进的隧道式感应加热炉已得到大量应用。隧道式感应加热炉(见图3)是用于金属熔炼效率最高的电炉之一,在世界先进的有色及黑色金属铸造厂都可以见到。与螺线管形式感应器的无芯感应加热炉相比,它采用了一种隧道形式的带有铁芯的感应器,其工作原理就如同一个变压器,该隧道式感应器就是变压器的初级线圈,坩埚内的熔融金属就是变压器的次级线圈。由于感应器与熔融金属的耦合较紧,加热过程中功率因数很高,电能的利用率也非常高,可实现节约能源的目标;另外,由于电磁搅拌的作用效果非常好,熔融金属的成分均匀性也非常好,得到了用户的高度认可。除用于普通的铸造生产还可用于压力铸造的在线生产。
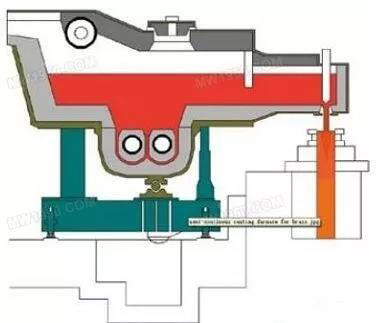
2. 金属半固态成形中感应加热技术的应用
随着全球性能源危机,汽车轻量化显得尤为重要,在汽车制造中铝合金及一些轻合金的应用越来越多。为了提高这些轻金属的强度,对铝制零件的内在质量要求也越来越高,一种能够改善金属内部组织结构的半固态成形技术得到了广泛的应用。美国的INDUCTOHEAT、AMERITHERM、ELECTROHEAT、BONE FRONTIER等公司介绍了感应加热半固态成形技术(见图4)。半固态成形的概念就是首先将制备好的坯料加热到较低熔点的温度,此时的组织状态是细小球状颗粒和液态的混合相,然后这种半固态的液体注入到成型的模腔中成形,在结晶过程中每个细小的球状颗粒都可以作为一个晶核长大完成结晶过程,其最终的组织结构是细密均匀的球状组织,与传统铸造的树枝状结晶组织有很大区别。之所以能够得到球状组织,在加热过程中需要利用搅拌的手段,使半熔融金属中的固态颗粒进行球化,且在液态中分布均匀。而用感应加热方式即将金属加热到所需的温度,另外在交变磁场的作用下,还可以得到电磁搅拌的效果,因此该技术广泛用于电磁连铸生产过程。该技术的优点有以下几个方面:
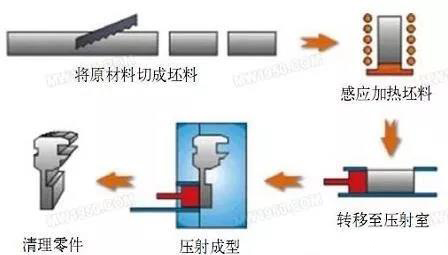
(1)高效节能,易于实现机械化和自动化,生产过程稳定,质量一致性好。
(2)生产效率高,可以与压铸生产保持同步。
(3)可以减少进入模腔的气体,铸件的缩孔、疏松等质量缺陷少。
(4)铸件的组织细密、均匀,强度有很大提高。
(5)混合液体的温度较低,降低了对模具的热冲击,从而有效地提高了模具寿命。
3. 汽车齿轮仿形双频感应淬火技术的应用
齿轮轮齿在载荷的作用下,轮齿根部的弯曲应力最大,同时在齿根部与轮缘的过度部分由于形状和尺寸的急剧变化产生应力集中。另外,由于在齿轮的啮合过程中轮齿的接触面积很小(理论上是线接触),在载荷的作用下,在齿面将产生很大的脉动变化的接触压应力,所以齿圈的失效形式主要是轮齿折断、齿面损坏和塑性变形。为了提高汽车齿轮的耐磨性和弯曲强度,要求齿轮的齿部表面和齿根表面具有较高的硬度和表面压应力;而为了避免产生脆性断裂,提高轮齿的韧性,心部硬度不易过高。目前广泛用于汽车齿轮的热处理方法有渗碳淬火和氮化处理。渗碳处理可以满足上述性能要求,但存在生产周期长、效率低、热处理变形控制困难,以及生产成本高等不足。氮化处理也存在生产周期长、效率低、生产成本高等不足,由于硬化层较薄,对提高耐磨性的作用较大,但对提高强度的作用则很小。
鉴于上述情况,美国的INDUCTOHEAT等公司介绍了齿轮单圈感应器双频感应淬火(single coil dualfrequency gear hardening)技术,该技术使用一个感应器,两套感应加热电源,其中一套频率为10~25kHz ,功率根据齿轮的尺寸和模数大小确定,用于齿根部分的加热,另外一套电源的频率为150~350kHz ,功率根据齿轮的尺寸和模数大小确定,但该功率是较低频率电源的2~3倍。采用分时段加热的方式,首先使用较低频率电源,比功率为2~4kW/cm2,将工件加热至低于奥氏体化温度50~100℃时立即停止加热,改用另外一个频率较高的电源给感应器供电,比功率为6~10kW/cm2用于加热齿顶部分,瞬间使加热温度达到高于奥氏体化温度80~100℃,停止加热(见图5),并立即喷水冷却,完成淬火过程,得到有效硬化层仿形分布的效果。
德国ELDEC等公司介绍了s imu l t a n e o u s d u a lfrequency gear hardening技术。该技术使用一个感应器,一套频率分别为10~25kHz和150~350kHz的双频感应加热电源,功率根据齿轮的尺寸和模数大小确定,采用同时加热的方式,即在同一个感应器内通有上述两种频率的交变电流,比功率一般在15~20kW/cm2,根据零件的尺寸和模数通过试验确定,在极短的时间内(0.2~1.5s)完成齿根、齿面和齿根的加热过程,并立即喷水进行冷却,完成淬火过程,同样得到有效硬化层仿形分布淬火的效果(见图6)。汽车齿轮仿形双频感应淬火技术优点是,加热时间短,生产效率高,零件的淬火变形小,设备的占地面积少,生产环境清洁无污染,机械化、自动化程度高,可与其他加工设备共线生产。
4. 感应加热技术在非金属粉末涂敷中的应用
为了减小汽车传动轴花键轴叉和花键套管间的摩擦系数,降低噪声,提高整车的可靠性和耐久性,借鉴国外样车的成功经验,经对标分析发现,在花键套管与花键轴叉的配合位置做了局部尼龙涂敷,采用的是热涂敷工艺。用炉中加热方式存在以下不足:
(1) 需要将零件整体加热,工艺周期长,为满足生产节拍,设备占地面积大。
(2)只需要局部涂敷,其余部分要进行防护,导致工序复杂。
(3)为了满足工艺节拍的要求,保证零件到达涂敷工位的工艺温度,需要工件有较高的过热度,导致工件的表面氧化,降低涂敷材料和零件间的附着力, 影响涂敷质量。
为此,一汽集团公司应用感应加热技术,利用感应加热可以实现零件局部加热的特点,采用合理的工艺方法和工艺参数,严格控制加热区域和加热温度,减少了零件在涂敷前的氧化,不需涂敷的部分大大低于工艺温度,不用采取任何防护措施。设备的占地面积小,自动化程度高,可根据涂敷工序的时间合理安排感应加热的节拍,并实现了在线生产,涂敷后实物见图7。该工艺提高了生产效率,降低了能耗和工艺成本,改善了生产环境,取得了较好的经济效益和社会效益,具有广泛的推广应用前景。
5. 感应加热技术在高强钢板成形及热处理中的应用
为了提高汽车车身的安全性及实现轻量化的目标,欧美及日本等汽车制造技术比较先进的各汽车厂家,争相采用减薄高强钢板,通过热处理强化的方式,提高车身结构件的强度。通常的做法是,使用为满足车身板热处理需求而开发的专用钢板。该材料应具有淬硬性能好、在高温晶粒长大速度慢、组织细密等性能,在进行冲压成形前使其在加热炉中加热到奥氏体化温度以上50~80℃,然后快速送到模具内成形,利用带有冷却水道的模具使其迅速冷却到马氏体相变点以下温度,进行马氏体转变,实现淬火过程。目前的加热方式一般采用带有快速送料机构的缝隙式加热炉进行加热,为了减少加热过程中的氧化,炉内还要用惰性气体或保护气氛加以保护。经这样处理后的车身结构件(如A、B、C柱及副车架等,见图8)的抗拉强度能够达到1300~1500MPa,提高近2~3倍,因而在实现了轻量化的情况下,大大提高了汽车的安全性。
据资料介绍,日本的高周波热炼等公司利用感应加热速度快的特点,成功开发了用感应加热代替广泛使用的炉中加热新技术。该技术具有加热速度快,电热转换效率高,设备占地面积少,机械化和自动化程度高,以及能够与生产线共线生产等优点,并在生产中得到应用。
三、结语
随着中国经济的高速发展和对环境保护的高度重视,在全球性能源紧张的背景下,节能、环保是汽车制造业要面对的两个非常重要的现实问题。作为一种高效、污染小的加热方式,感应加热技术在汽车制造领域将会得到越来越广泛的应用。
AMTS 2018 第十四届上海国际汽车制造技术与装备及材料展览会将于2018年7月4-7日在上海举行,将汇聚来自中国/亚洲的知名汽车制造商和一级供应商的工程技术人员和决策者到场参观,预计将有来自世界各地800家展商参展,吸引80,000专业观众到场参观。
获取更多AMTS 2018展会信息:
邮箱:info@for-expo.com
电话:86-21-6468 1300/6468 1550